BioCloner Project
Innovation shaping the future
Meet BioCloner 3D
BioCloner is not only a multifunctional 3D bioprinter dedicated to producing structures used in tissue engineering.
BioCloner is, above all, a technological concept that has been developed in our company since 2016. This concept will, in the coming years, enable significant improvements in the quality of life and health of both people and animals through the creation of innovative solutions dedicated to broadly understood medicine and veterinary science. Want to know more? Contact us!
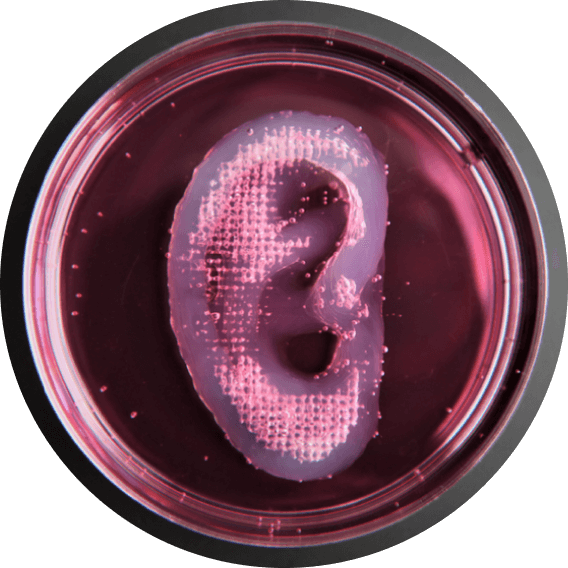
BioCloner 1.0
Currently, 3D bioprinting is one of the fastest-growing branches of modern regenerative medicine.
Every day, new solutions and materials emerge on the market, which in the near future will enable the production of tissue structures that can save the lives and health of both humans and animals. In response to the inevitable progress of technology and in line with market expectations, we have developed a unique solution tailored to the dynamically changing world.
BioCloner 1.0 is ready to carry out production work using multiple print heads, and as a result, different materials within a single process. The accuracy of print continuity is ensured by a dedicated calibration system. This is a vision-based solution that controls the actual position of the print nozzle. Thanks to this, each time a print head is changed, we are assured that the new head will operate in the same reference frame as the previous one.
All processes, both manufacturing and supporting (such as print nozzle cleaning, calibration, etc.), take place in an integrated, cleanroom environment. BioCloner 1.0 has been designed and constructed to efficiently separate the machine's drive systems from the working space.
This solution is primarily aimed at limiting the unwanted access of contaminants, both solid and liquid, such as lubricants or metal particles. Additionally, the enhanced cleanliness in the working area is maintained through germicidal UV lamps and a horizontal air intake system based on HEPA filters. This setup ensures overpressure in the workspace, which indirectly acts as a barrier against excessive contamination of the working environment.
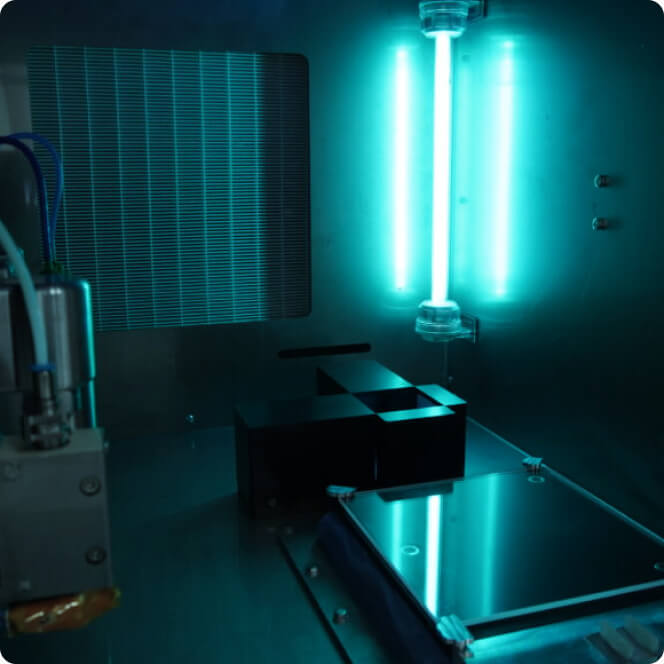
Multifunctional print heads
BioCloner 1.0 features an automated print head exchange system during the process.
This allows a single print to consist of many different materials in the form of granules, filaments, gels, or liquids. Below are the heads dedicated to the device:
-
High-temperature pressure print head
- A print head primarily dedicated to working with thermoplastics in the form of granules or powder.
- Maximum operating temperature up to 250°C.
- Printing can be carried out using print nozzles with diameters ranging from 0.1 to 0.8 mm.
-
High-temperature screw print head
- A print head primarily dedicated to working with thermoplastics in the form of granules or powder.
- Maximum operating temperature up to 250°C.
- Printing can be carried out using print nozzles with diameters ranging from 0.1 to 0.8 mm.
-
High-temperature pressure print head
- A print head primarily dedicated to working with materials in liquid or gel form.
- The operating temperature range is from 25 to 60°C.
- Printing can be carried out using print nozzles with diameters ranging from 0.1 to 1.2 mm.
- The print head can also be equipped with a crosslinking system in the form of a UV diode or a nozzle for spraying a crosslinking agent.
-
Calibration print head
- A supporting print head, primarily aimed at ensuring the accuracy of the process.
- Its task is both to calibrate the working table and to perform a reference measurement of the calibration bed.
-
Filament print head
- A supporting print head, primarily aimed at ensuring the accuracy of the process.
- Its task is both to calibrate the working table and to perform a reference measurement of the calibration bed.
Dedicated software
Our software consists of several modules that allow for working with the printer at different stages – from design to the creation of the final product.
A special application launched in a web browser allows for loading a 3D model into the virtual workspace, modifying it, and selecting print parameters. As a result, we get a view of the model divided into layers and a generated g-code enabling model printing. The application also allows remote monitoring of the device's status.
To fully harness the potential of innovative mechanical and hardware solutions, we are also developing our own fully customizable software that directly controls the operation of the printers. In addition to generating g-code during the design stage, it is also responsible for executing the printing process of the previously prepared model. It also manages safety systems that ensure secure operation for the user while working with the machine.
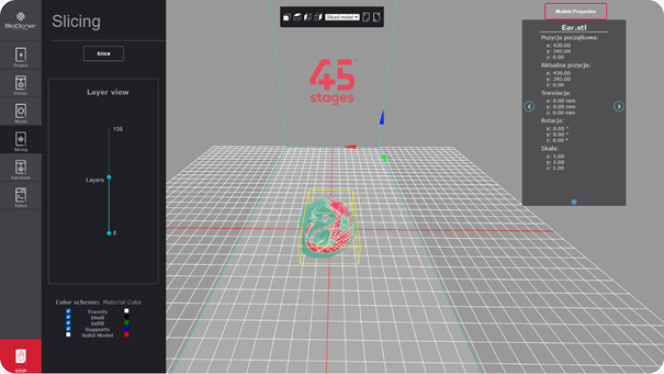
Innovative solutions require a creative approach!
Our implementation and development in the field of 3D bioprinting is the result of a fantastic interdisciplinary team. Thanks to the versatility of our small family, we were able to develop our own solutions in the fields of mechanics, industrial automation, and programming.
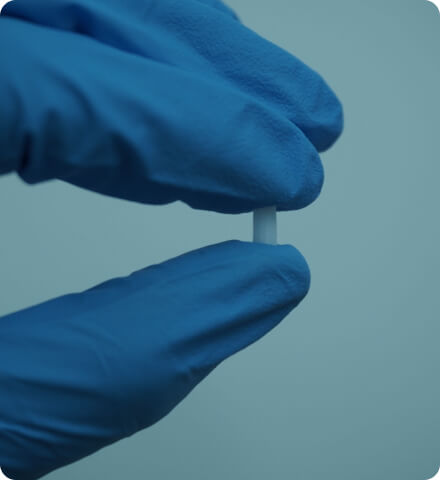
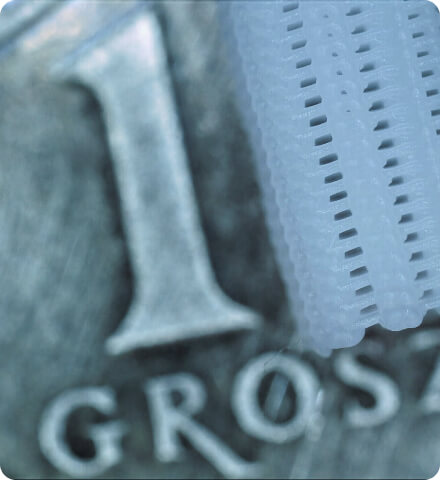
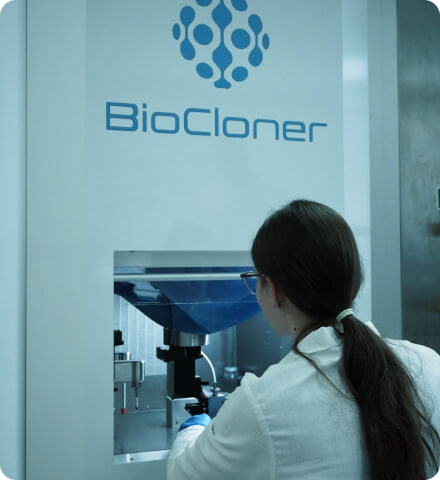
Step by step towards innovation
-
september 2016
Start of the BioCloner project
Thanks to funding from the European Union, we were able to start realizing our vision. The plan was simple. First, we had to build everything from scratch.
Since then, all efforts have been focused on the development of our solutions for mechanics, automation, and software. -
2016
Project R&D phase
Hundreds of concepts, thousands of tests, all to discover new possibilities. Day by day, we strive to improve our solutions. We hope that each day brings us closer to achieving our goal, which is the introduction of innovative solutions for medicine and veterinary science.
-
december 2017
The first fully functional prototype was created
-
november 2018
A fully functional 3D bioprinting laboratory was established.
-
november 2019
Securing a strategic investor - Valegro Limited
-
2020 – present
Implementation and transformation of technology
If you want to learn more, follow us on our LinkedIn.
Let's work together!
Want to shape the future together? Contact us or visit us on LinkedIn!
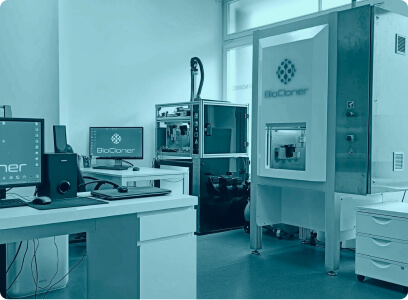